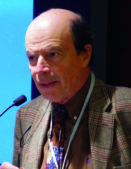
In this issue of our magazine, which is growing in following due to its amount of valuable contributions, we will address the topics of service and of the progress related to the improvement of diagnostic investigation techniques: in terms of the infrastructures and technologies available in the field, as well as the increasingly smarter computer tools that make the huge amounts of data (big and transversal…) that come from the plants usable.
When the team involved and the evaluation elements introduced in the plants (nowadays the “I.O.T.” is broadly used to connect the various assets) manage to create a synergistic dialogue, the results obtained are often far more reliable and efficient than expected. As I said in the past, it is essential to give the right credit to the winning team, recognizing their achievements.
As a consequence of certain predictive choices, there have been unexpected relapses (actual surprises) that make this challenge even more stimulating, which was initially based on establishing a system of control of the root causes of failure. In this preface to this month’s articles, I would like to tell you about the unimaginable managerial advantages that derived from our practical experience of conditions monitoring techniques through the analysis of lubricating oils.
When we first started to consider the “tribological monitoring” of lubricants – wording that to this day I am not convinced was the most correct, but people liked it and it stuck – in the early 90s, not many people subscribed to such a project. Let’s say that from the point of view of the traditional maintenance operators, who acted upon equipment “breakdown”, there was a lot of distrust towards a methodology that was seen as too sophisticated to be applied to large industrial complexes. Thinking that the creeping enemy of a machine weighing several tonnes, with hundreds of liters of oil in its belly, could be barely visible particles whose severity could only be rated by a third party, was heresy. The available technique – more suitable for traditional medicine than engineering – was still in its infancy, but already showed promising results. Granted that someone would trust us, giving permission to carry out a simple test.
The first tests were classified by some people as used oil analysis, often leading to the disposal of lubricating products that were still in perfect condition. After all, at the time the new was preferred to recycling. But at the same time we could feel the desire on the part of some of the more evolved figures to face a new challenge, to explore firsthand with us the potential of a refined investigation, able to amplify the weak signals in a drop of oil, and face decisions of strategic importance. At the same time, high performance PCs were being developed and the Internet allowed for rapid communication, so we could make make just-in-time decisions capable of halting the progress of failures that could otherwise become catastrophic. And thanks to a few lucky breaks – which was actually background work of processing very complex data without an established historical archive – we managed to overcome the uncertain phase by creating the basis for a methodological approach, which later became an actual internationally standardized discipline. One of the most notable downfalls (not obvious at that stage) has now become a subject of great media attention.
We talk about Sustainability; a topic that has grown in popularity since we discovered (we hypocritically say that it was recently, but in fact we have all been well aware of it for a long time) that the world’s resources are “finite” and our consumption model must be rebalanced.
The cultural growth of the people involved, combined with the pressing need to limit consumption of raw materials, has led to a new awareness when it comes to plant management. The filtration of fluids, hydraulic and lubricants, has become a procedure that is appreciated and even recommended by plant manufacturers, starting from the idea that even new materials are not free of defects. And the invisible contamination is just as bad as the macroscopic one. This process is mainly cultural, where technology has brought many contributions, including a new focus on lubricants in general. These products have become innovative, widely consumed and must be carefully stored, guaranteeing a longer useful life to the benefit of an increasingly fragile environment.
When we started our unrecognized work 35 years ago – they really were different times – we coined this slogan (a piece of history, which has now become a cornerstone of the Italian Predictive Maintenance): “This drop of oil contains a precious message”. For the now well-known technical and practical reasons, but back then Sustainability did not seem to be a priority!
The significant benefits – sometimes unexpected – of conditions monitoring – Extract from the magazine AIMAN – MANUTENZIONE & ASSET MANAGEMENT, MARCH 2024
Article by: Giuseppe Adriani, Member of the Board of Directors and regional coordinator of A.I.MAN. Toscana
[ITALIAN ONLY] EDITORIALE_MANUTENZIONE & ASSET MANAGEMENT MARZO 24